Fondamenti dei moduli IGBT ad alta tensione
Struttura di base e meccanismo di commutazione
L'alta tensione Modulo del transistor bipolare con gate isolato (IGBT) è un capolavoro di ingegneria elettronica di potenza, che unisce una progettazione precisa dei semiconduttori a un packaging resistente, in grado di sopportare sollecitazioni elettriche estreme. La sua struttura principale è un'interazione sinergica di tre sottosistemi chiave: il die semiconduttore di potenza, l'elettronica di controllo di gate e l'interfaccia di gestione termica, ciascuno ottimizzato per bilanciare la capacità di sopportare alte tensioni con un'interruzione rapida.
Al cuore del sistema si trova il Chip IGBT , generalmente realizzato in silicio (Si) grazie all'ecosistema produttivo ormai maturo, sebbene materiali emergenti a banda proibita larga come il carburo di silicio (SiC) stiano prendendo piede per garantire un'efficienza superiore. I chip moderni utilizzano la tecnologia field-stop (FS) , una svolta nel blocco della tensione: uno strato sottile e fortemente drogato vicino al collettore "pinza" il campo elettrico nella regione di deriva, riducendo lo spessore del chip pur mantenendo un'elevata capacità di tensione. Ad esempio, un chip FS-IGBT da 6500V raggiunge la sua capacità di blocco con uno strato di deriva del 30% più sottile rispetto ai vecchi design non punch-through (NPT), riducendo le perdite di conduzione del 15-20%.
Il driver di gate è il "cervello" del modulo, che traduce i segnali di controllo a bassa tensione (5-15V) nelle azioni ad alta tensione dell'IGBT. Per evitare interferenze di rumore tra il circuito di controllo (bassa tensione) e il circuito di potenza, i gate driver utilizzano isolamento galvanico —ottica (tramite collegamenti in fibra ottica) o magnetica (tramite trasformatori di impulso). L'isolamento ottico offre tempi di risposta più rapidi (<100ns) e una migliore immunità al rumore, rendendola ideale per applicazioni ad alta frequenza come i STATCOM, mentre l'isolamento magnetico è più economico per scenari a bassa frequenza, come gli azionamenti industriali. I driver avanzati integrano inoltre funzioni di protezione: il blocco in assenza di tensione (UVLO) spegne l'IGBT se la tensione di gate scende al di sotto di 12V, evitando danni dovuti a un'accensione incompleta; il rilevamento di desaturazione individua il sovraccarico monitorando la tensione collettore-emettitore (VCE), attivando uno spegnimento graduale in <1µs.
Il confezionamento è l'ultimo strato critico, che contiene il chip e il driver garantendo al contempo il dissipamento del calore. I moduli ad alta tensione utilizzano substrati ceramici â (ad esempio Alâ‚‚O₃ o AlN) per isolare elettricamente il chip dal dissipatore, conducendo al contempo il calore. I substrati in AlN, con una conducibilità termica 5 volte superiore rispetto all'Alâ‚‚O₃, sono preferiti per moduli a 6500V nei sistemi HVDC, dove il flusso termico supera i 50W/cm². L'incapsulante, spesso un gel di silicone o un'epossidica, protegge le componenti interne dall'umidità e dalle sollecitazioni meccaniche, garantendo affidabilità in ambienti difficili come gallerie ferroviarie o parchi solari desertici.
Capacità di gestione della tensione (range da 1700V a 6500V)
Alta tensione Moduli IGBT sono progettati per operare efficacemente nell'intervallo 1700V-6500V, una versatilità derivata da un'accurata progettazione dei chip e dall'uso di materiali specifici. Ogni classe di tensione è mirata ad applicazioni distinte, con margini costruttivi per sopravvivere a picchi transitori, essenziali per evitare guasti catastrofici.
moduli a 1700V : Dominante nelle energie rinnovabili e nei sistemi di trazione industriale. Nei convertitori solari a 1500V, gestiscono tensioni DC-link fino a 1800V (con un margine di sicurezza del 20% per picchi di tensione dovuti a condizioni atmosferiche) e commutano a 16-20kHz per minimizzare la distorsione armonica. Alimentano inoltre sistemi di trazione industriale AC a 400V per pompe e ventilatori, dove la loro bassa tensione in conduzione (VCE(sat) <1,8V alla corrente nominale) riduce le perdite per conduzione.
moduli a 3300V : Il cavallo da soma dei sistemi a media tensione. Sono essenziali per le linee aeree ferroviarie in corrente continua a 3 kV, convertendo la corrente continua in corrente alternata trifase per i motori di trazione nei treni come l'ICE 4 di Germania, che utilizza moduli a 3300 V/1200 A per raggiungere velocità di 300 km/h. Nei generatori eolici, i moduli a 3300 V permettono convertitori da 6 MW+, gestendo l'uscita in corrente continua variabile dei generatori e sincronizzandosi con la rete elettrica.
moduli da 4500V a 6500V : Riservati a applicazioni su scala della rete elettrica. I moduli a 4500 V alimentano azionamenti industriali a 6-10 kV nelle acciaierie, dove resistono a sovraccarichi 5 volte superiori per 10 secondi durante il funzionamento di punta. I moduli a 6500 V costituiscono la spina dorsale della trasmissione in corrente continua ad alta tensione (HVDC): il progetto HVDC Xiangjiaba-Shanghai in Cina, a ±800 kV, utilizza moduli a 6500 V/2500 A nei suoi convertitori, trasmettendo 6,4 GW di elettricità su 1900 km con perdite totali inferiori al 7%.
Un fattore chiave nella loro resistenza alla tensione è robustezza in valanga —la capacità di resistere a sovratensioni temporanee consentendo un breakdown controllato ad avalanche. I moduli a 6500V, ad esempio, possono sopravvivere a eventi di avalanche di 7000V per 10µs, una protezione fondamentale contro i fulmini nelle linee aeree.
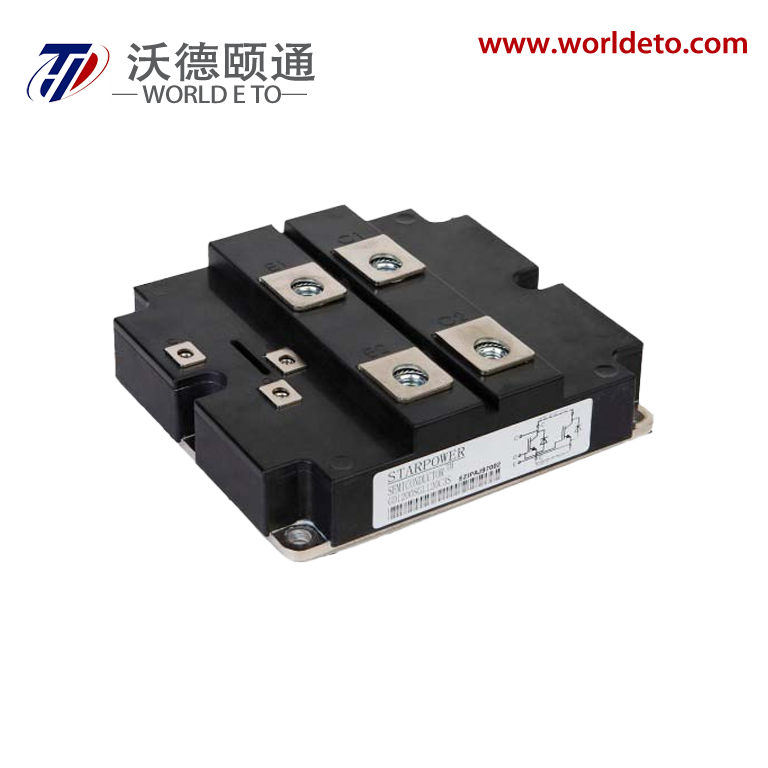
Applicazioni nelle infrastrutture della rete elettrica
Sistemi di trasmissione HVDC
I sistemi a corrente continua ad alta tensione (HVDC) stanno rivoluzionando la trasmissione di energia elettrica a lunga distanza, e i moduli IGBT ne sono il motore. A differenza della trasmissione in corrente alternata, che perde il 15-20% dell'energia su una distanza di 1000 km, l'HVDC con IGBT riduce le perdite al 5-8%, grazie a due vantaggi chiave:
Conversione efficiente dell'energia : I convertitori a sorgente di tensione (VSC) basati su IGBT sostituiscono i convertitori line-commutati (LCC) basati su tiristori, permettendo un flusso di potenza bidirezionale e una stabilizzazione più rapida della rete. Ad esempio, il progetto HVDC Western Link del Regno Unito utilizza IGBT a 6500V per trasmettere 2GW di energia eolica dalla Scozia all'Inghilterra, regolando il flusso di potenza in meno di 10ms per bilanciare la domanda sulla rete.
Minori Richieste di Spazio per l'Infrastruttura : L’HVDC richiede meno conduttori rispetto alla corrente alternata (1-2 per la corrente continua contro 3 per quella alternata), risultando ideale per cavi sottomarini — il progetto NordLink della Norvegia utilizza un cavo HVDC sottomarino di 510km con convertitori IGBT per scambiare energia idroelettrica con la Germania, minimizzando l'impatto ambientale.
STATCOM per la Stabilizzazione della Rete
S i compensatori sincroni statici (STATCOM) sono gli "ammortizzatori" della rete e gli IGBT forniscono una velocità senza precedenti. Nelle reti con elevata penetrazione di rinnovabili (ad esempio, 30%+ di eolico/solare), le fluttuazioni di tensione sono comuni: un'improvvisa copertura nuvolosa può ridurre l'output solare del 50% in pochi secondi, causando cali di tensione. I STATCOM contrastano questo fenomeno iniettando potenza reattiva (MVAr) per aumentare la tensione, con gli IGBT che permettono tempi di risposta inferiori a 5 ms (10 volte più veloci rispetto ai tradizionali banchi di condensatori).
Un STATCOM basato su IGBT a 3300V nella rete ERCOT del Texas, ad esempio, mantiene la tensione entro ±1% del valore nominale regolando la potenza reattiva da -100 MVAr a +100 MVAr, prevenendo i blackout durante cali di vento causati da tempeste. Questa capacità è il motivo per cui reti in tutto il mondo - dal Gujarat in India, ricco di fonti rinnovabili, al National Electricity Market dell'Australia - stanno installando STATCOM IGBT a un ritmo di 5-10 GW/anno.
Applicazioni Ferroviarie
Inverter di Propulsione e Frenatura Rigenerativa
Le ferrovie richiedono IGBT in grado di unire elevate prestazioni a robustezza, e i moduli a 3300V soddisfano entrambi i requisiti. Nei treni ad alta velocità, gli inverter di trazione convertono la tensione continua della linea aerea (1,5 kV o 3 kV) in corrente alternata a frequenza variabile per i motori di trazione, con gli IGBT che commutano a 2-5 kHz per garantire un'accelerazione regolare. Lo Shinkansen N700S del Giappone utilizza moduli a 3300V/1500A per raggiungere i 360 km/h, con meno del 3% di ripple di coppia per il comfort dei passeggeri.
Il freno rigenerativo rappresenta il campo di eccellenza degli IGBT: durante la decelerazione, i motori di trazione agiscono come generatori, convertendo l'energia cinetica in elettricità. Gli IGBT riconvertono questa corrente alternata in corrente continua, immessa nuovamente nella linea aerea per essere utilizzata da altri treni. Nella linea Yamanote di Tokyo, questo sistema recupera circa il 30% dell'energia, riducendo il consumo annuale dalla rete di 18 GWh e aumentando la durata delle pastiglie dei freni del 60%.
Robustezza ambientale
L'ambiente ferroviario è estremamente impegnativo: vibrazioni (fino a 20g), escursioni termiche (-40°C a +85°C) e polvere/detriti rappresentano costantemente una minaccia. I moduli IGBT per applicazioni ferroviarie sono progettati per resistere a tutto questo:
Resistenza alle vibrazioni : Utilizza l'ancoraggio senza saldatura (ad esempio, sinterizzazione con argento) invece della saldatura tradizionale, che può rompersi sotto vibrazioni. I legami sinterizzati con argento hanno una conducibilità termica 3 volte superiore e resistono a 100 milioni di cicli di vibrazione (secondo IEC 61373) senza degradazione.
Resilienza Termica raffreddamento doppio con liquido refrigerante (miscela glicole-acqua) mantiene le temperature di giunzione al di sotto dei 125°C anche in climi desertici o artici. Il treno ad alta velocità CRH2A, che opera nella provincia cinese di Heilongjiang a -40°C, utilizza questa soluzione per garantire prestazioni affidabili.
Soluzioni di Gestione Termica
Il calore è il principale nemico degli IGBT: temperature eccessive accelerano l'invecchiamento, riducono la capacità di bloccare la tensione e possono causare guasti immediati. Un avanzato sistema di gestione termica assicura che i moduli operino all'interno del loro intervallo di temperatura sicuro (tipicamente tra -40°C e +150°C per la temperatura di giunzione).
Materiali di Interfaccia Termica (TIMs) questi materiali riempiono i microspazi tra il modulo e il dissipatore, riducendo la resistenza termica. I TIM tradizionali (ad esempio pasta termica) offrono una conducibilità di 1-3 W/m·K, ma soluzioni moderne come dischi rinforzati con grafene arrivano a 10-15 W/m·K. In moduli HVDC a 6500 V, ciò riduce la resistenza termica tra giunzione e dissipatore del 40%, abbassando la temperatura operativa di 15-20°C.
Raffreddamento Bilaterale : Invece di raffreddare soltanto la piastra di base, questa soluzione prevede la circolazione del liquido refrigerante su entrambi i lati del modulo. Per moduli ferroviari a 3300 V, raddoppia la capacità di dissipazione del calore, permettendo un aumento del 20% della corrente in uscita senza surriscaldamento.
Micro-Dissipatori : I moduli compatti (ad esempio per locomotive elettriche) utilizzano dissipatori di calore a microcanali con canali di 50-200µm, attraverso i quali scorre il refrigerante a una velocità di 2-3m/s. Questo consente di raggiungere densità di flusso termico di 100W/cm² â essenziale per applicazioni con limitazioni di spazio dove non è possibile installare grandi dissipatori.
Meccanismi di protezione
Gli ambienti ad alta tensione sono soggetti a guasti â sovratensione, sovracorrente e cortocircuiti. I moduli IGBT integrano multiple protezioni per sopravvivere a questi eventi:
Limitazione della sovratensione : I varistori a ossido metallico (MOVs) o i suppressori di tensione transitoria (TVS) deviano la tensione in eccesso verso terra. Un modulo da 6500V potrebbe utilizzare un MOV da 7000V, limitando le sovratensioni causate da fulmini o da commutazione di carichi induttivi in meno di 10ns.
Resistenza al cortocircuito : Gli IGBT possono sopportare cortocircuiti per 10-100µs (a seconda della classe). Durante un cortocircuito, il gate driver rileva l'aumento di VCE (desaturazione) e applica una tensione negativa (-5V) per spegnere il dispositivo, limitando la dissipazione di energia. I moduli a 3300V sopravvivono tipicamente a 4 volte la corrente nominale per 50µs.
Miglioramento della RBSOA : La Safe Operating Area per il Blocco Ripetitivo (RBSOA) definisce le condizioni in cui l'IGBT può bloccare la tensione dopo un cortocircuito. I moderni FS-IGBT espandono la RBSOA, permettendo di bloccare l'intera tensione anche con una corrente pari a 2x quella nominale—fondamentale per il recupero da guasti sulla rete.
Ingegneria della Affidabilità
L'affidabilità a lungo termine è fondamentale per gli IGBT in applicazioni critiche (ad esempio ospedali, centrali nucleari). Due fattori chiave garantiscono questo risultato:
Capacità di ciclo di potenza : I moduli devono sopravvivere a cicli ripetuti di riscaldamento/raffreddamento (ÎTj = 50-100°C). Soluzioni avanzate con interconnessioni in alluminio (anziché oro) e basi in rame raggiungono oltre 1 milione di cicli, estendendo la vita utile a 15-20 anni nei sistemi industriali.
Resistenza all'umidità : Le applicazioni esterne (es. turbine eoliche) sono esposte a elevata umidità, che può causare corrosione o correnti di dispersione. Moduli con involucri IP67 e rivestimenti conformi in parylene sopravvivono a 1000 ore a 85°C/85%RH (secondo IEC 60068) con deriva dei parametri <10%.
Applicazioni emergenti
Azionamenti a Media Tensione : IGBT da 4500V in azionamenti 6-10kV per mulini cementizi e pompe idrauliche aumentano l'efficienza dal 95% al 98%, risparmiando il 3-5% sui costi energetici. Ad esempio, un azionamento da 10MW in un impianto di dissalazione in Arabia Saudita riduce il consumo annuo di elettricità di 4,2 GWh.
Integrazione delle Fonti Rinnovabili : I moduli a 1700V permettono inverter solari da 300kW+ con efficienza del 99,2%, mentre i moduli a 3300V nei convertitori per turbine eoliche offshore da 15MW gestiscono l'output variabile di turbine da 12MW, garantendo una stabile integrazione alla rete.
Domande Frequenti
Quando dovrei scegliere IGBT al carburo di silicio (SiC) invece degli IGBT tradizionali al silicio (Si)?
Gli IGBT al carburo di silicio (SiC) offrono minori perdite di conduzione/commutazione e una maggiore tolleranza alle temperature (fino a 200°C), rendendoli ideali per applicazioni ad alta frequenza (ad esempio, inverter solari a 20kHz+). Tuttavia, il loro costo è 2-3 volte superiore rispetto al silicio (Si), motivo per cui quest'ultimo rimane preferibile per utilizzi a bassa frequenza e sensibili al costo (ad esempio, HVDC).
Gli IGBT al carburo di silicio (SiC) offrono minori perdite di conduzione/commutazione e una maggiore tolleranza alle temperature (fino a 200°C), rendendoli ideali per applicazioni ad alta frequenza (ad esempio, inverter solari a 20kHz+). Tuttavia, il loro costo è 2-3 volte superiore rispetto al silicio (Si), motivo per cui quest'ultimo rimane preferibile per utilizzi a bassa frequenza e sensibili al costo (ad esempio, HVDC).
Come testare un Modulo IGBT per guasti?
Utilizzare un multimetro per verificare eventuali cortocircuiti tra collettore-emettitore (dovrebbe mostrare resistenza infinita quando spento) e gate-emettitore (5-10kΩ). Per test dinamici, un oscilloscopio misura VCE e la corrente durante la commutazione, per rilevare picchi di tensione eccessivi o un tempo di spegnimento troppo lento.
Utilizzare un multimetro per verificare eventuali cortocircuiti tra collettore-emettitore (dovrebbe mostrare resistenza infinita quando spento) e gate-emettitore (5-10kΩ). Per test dinamici, un oscilloscopio misura VCE e la corrente durante la commutazione, per rilevare picchi di tensione eccessivi o un tempo di spegnimento troppo lento.
Qual è l'impatto della frequenza di commutazione sulle prestazioni degli IGBT?
La frequenza più alta riduce le dimensioni dei componenti passivi (induttori/condensatori) ma aumenta le perdite di commutazione. Per HVDC (50-100Hz), concentrarsi su basse perdite di conduzione; per STATCOMs (1-5kHz), dare priorità a commutazione rapida.
La frequenza più alta riduce le dimensioni dei componenti passivi (induttori/condensatori) ma aumenta le perdite di commutazione. Per HVDC (50-100Hz), concentrarsi su basse perdite di conduzione; per STATCOMs (1-5kHz), dare priorità a commutazione rapida.
Gli IGBT possono essere utilizzati nei veicoli elettrici (EV)?
Sì - IGBT da 1200V sono comuni negli inverter per veicoli elettrici (EV), che convertono la corrente continua della batteria in corrente alternata per il motore. La Model 3 di Tesla utilizza 24 IGBT nel proprio inverter, permettendo un funzionamento a 400V/600A con un'efficienza del 97%.
Sì - IGBT da 1200V sono comuni negli inverter per veicoli elettrici (EV), che convertono la corrente continua della batteria in corrente alternata per il motore. La Model 3 di Tesla utilizza 24 IGBT nel proprio inverter, permettendo un funzionamento a 400V/600A con un'efficienza del 97%.
Qual è il futuro degli IGBT ad alta tensione?
Le tendenze includono l'integrazione di SiC, tensioni nominali più elevate (10 kV+), e moduli più intelligenti con sensori integrati per il monitoraggio in tempo reale delle condizioni, essenziali per reti elettriche auto-riparanti e sistemi industriali autonomi.
Le tendenze includono l'integrazione di SiC, tensioni nominali più elevate (10 kV+), e moduli più intelligenti con sensori integrati per il monitoraggio in tempo reale delle condizioni, essenziali per reti elettriche auto-riparanti e sistemi industriali autonomi.
Indice
- Fondamenti dei moduli IGBT ad alta tensione
- Struttura di base e meccanismo di commutazione
- Capacità di gestione della tensione (range da 1700V a 6500V)
- Applicazioni nelle infrastrutture della rete elettrica
- Applicazioni Ferroviarie
- Soluzioni di Gestione Termica
- Meccanismi di protezione
- Ingegneria della Affidabilità
- Applicazioni emergenti
- Domande Frequenti